
External details, such as the thread and neck flange for a screw-top container, are directly produced by injection molding.
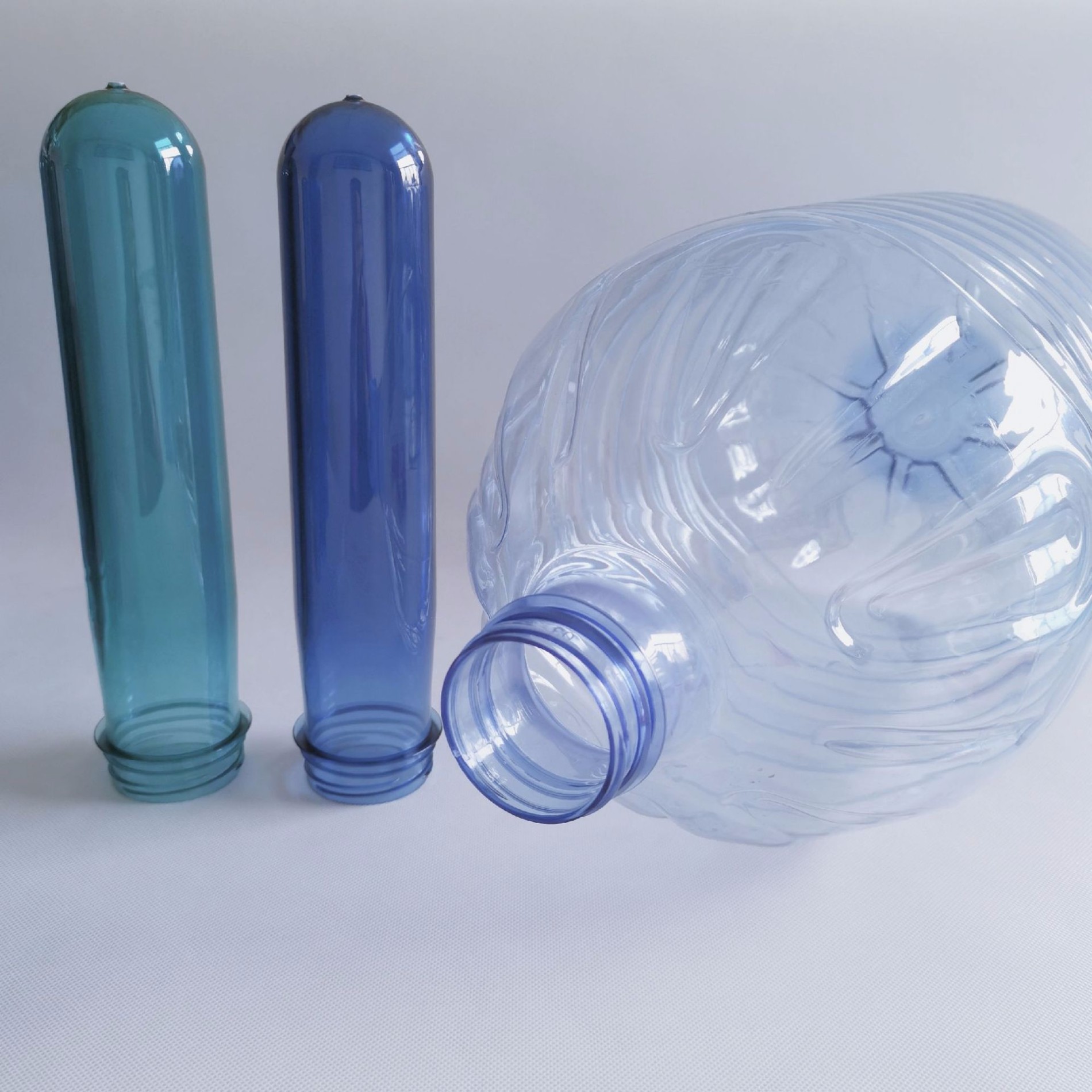
The other ends have an open bore, formed by the core pin. The preforms have hemispherical closed ends (resembles a laboratory test tube). Three station injection blow molding systemįirst station usually has multiple preform injection molds where preforms are formed over core pins. Improved oxygen barrier can be obtained by using barrier materials such as polyamides and polyvinyl alcohol, the former can be added as a monolayer, but usually the barrier (oxygen scavenger) is added as a separate layer in the centre of the preform.įigure 6.9. Very lightweight bottles with good moisture and carbon dioxide barrier and pressure resistance properties can be produced using this method. In this way the material is orientated in both directions this improves clarity, mechanical and barrier properties. Once in the blow mould, the stretch rod pushes the preform to the bottom of the blow mould, air is introduced through the rod which expands the preform to the shape of the blow mould. Both the rod and the preform are heated to a controlled constant temperature, usually just above the T g of the polymer, the bottle finish area being kept cool so that it does not distort.

In injection (the most common use) stretch blow moulding, the preheated preform held on the stretch rod is placed in the blow mould. Stretch blow moulding can be carried out on both injection and extrusion processes ( Fig. 14.39). To produce bottles suitable for carbonated beverages, the gas barrier and mechanical properties (tensile and burst strength) of the final bottle have to be greater than for a non-carbonated product not requiring a gas barrier. The coolant is usually water maintained at a constant temperature. The mould has cooling ducts incorporated into its design. Venting is necessary so that all trapped air is removed from between the moulding and the mould. Air is introduced via the preform neck and the preform is blown into the shape of the mould. Once moulded, the preform is reheated (different zones of the preform are heated to different temperatures to best suit the final blown form requirement) and placed in the blow mould.
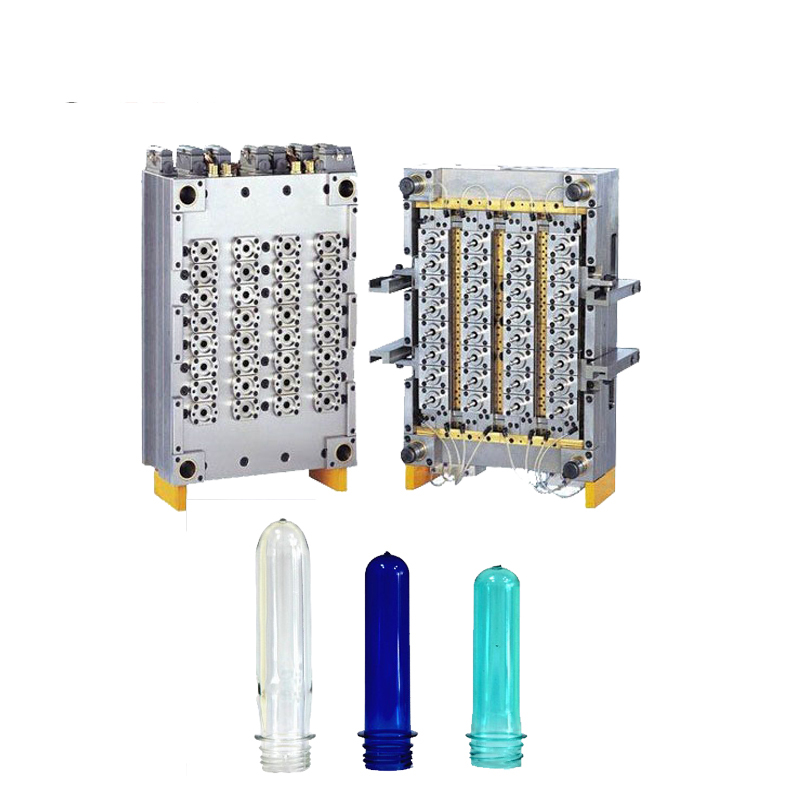
The preform is designed to have a profile and variable wall thickness to provide the correct mechanical and barrier properties in the final blown moulding. The preform is injection moulded as a separate stage, in a separate machine. The two-stage blow moulding process is used for standard and stretch blow moulded items ( Fig. 14.38).
